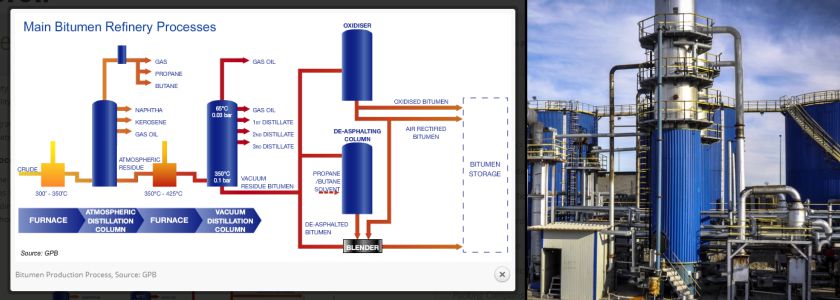
BITUMEN PRODUCTION PROCESS
Of the wide variety of crude oils commercially available, only a limited number are considered suitable for producing bitumen of the required quality in commercial quantities. In general, these are heavy crude oils with a high sulphur content.
In modern, integrated refineries, it is common practice to blend multiple crude oils to produce consistent quality high grade bitumen that meets precise engineering specifications.
Production processes
Residues from the distillation of meticulously selected crude oils provide the base materials for bitumen production. Bitumen refining separates the lighter fractions from the residues. Several manufacturing methods are used to produce specification bitumens depending on the crude source and processing capabilities available. Often a combination of processes is selected. The illustration shows a compilation of the main refinery processes employed.
Distillation
The most common refining process is straight reduction from crude or a crude blend, using atmospheric and vacuum distillation. In the diagram, atmospheric distillation is used to separate lighter petrochemical and fuel fractions from the non-boiling component at the bottom, known as an atmospheric residue. The lighter fractions, such as gas oil and fuel oils are fed to other refinery units. The atmospheric residue is retained for bitumen. To remove the last traces of the lighter fractions and avoid heat transformation of the molecules, the atmospheric residue is introduced into a vacuum distillation unit, here the pressure reduction lowers boiling temperatures and unwanted thermal cracking of the molecules can be avoided.
Solvent de-asphalting
Specific solvents can also be used to separate the lubricant and bitumen components of crude, without damaging their chemical structure. According to the solvent used – propane or butane – different categories of bitumen can be obtained. Along with finely controlled variations in the vacuum distillation process, these processes permit the production of bitumens with varying levels of penetration. This property and the softening point are the two fundamental defining characteristics of bitumens produced to engineering specifications. Further key physical properties are sensitivity to temperature and ageing, cohesion and elasticity, all of which are measured by precise tests.
Oxidation
Bitumen can be further processed by blowing air through it at elevated temperatures (280°C on average) to alter its physical properties for commercial applications. Oxidised bitumen covers two distinct types depending on the degree of oxidation: air rectified and oxidised. Oxidised bitumen has a distinctive consistency at room temperature and a rubbery nature which affects how it responds to stress, or imprint. The process of oxidation increases the stiffness and softening point of the bitumen and considerably alters key physical properties. Varying the length of the oxidation or air blowing process varies the extent of the reaction and produces distinctive end products. Oxidised bitumen is used in roofing applications, while air rectified bitumen is used in paving applications and some roofing applications.
Blending
The final bitumen product can be produced to technical specification either directly in the refining process or by blending bitumens with different physical properties. Blending of higher and lower viscosity residues in the required proportions may take place at the refinery, at terminals or at a third party facility, where blend components and finished products can be easily transported and distributed for use.